

A detailed description of each file type can be found within the Surfer 12 | Files Types | Description book. In the Contents tab, navigate to Surfer 12 | Files Types to find information on each file type supported by Surfer. This list, along with a detailed description of each file format can also be found in the Surfer Help.

Please let us know if there are additional import/export formats that you would like to see supported in future versions of Surfer. If you are using Surfer in combination with another program, we would be happy to help you determine the compatibility with the software.
#SURFER 12 EXPORT 3D FILES FULL#
Export each layer in map to its own folder in the KML/KMZĪ full list of the supported data files, grid files, and import/export file formats for Surfer 12 can be found on the Golden Software website, in the Surfer 12 Features Tour under Supported File Formats.This added functionality in Surfer will allow you to maximize your use of Surfer along with other programs. Export contours to KML, and Z value is the Object ID for each line in the KML Z value is saved as metadata to MIF/MID, SHP/DBF, G SB, GSI, BLN, BNA using the The addition for more of the formats makes it easier for Surfer to work with external applications and other software. On more complex parts, the Custom settings can quickly increase the file size of a part, causing the 3D printing software to get bogged down in calculations.The release of Surfer 12 has bro ught the inclusion of additional import/export formats. The Fine setting gives us the best mix of resolution and file size. In the example below, the Fine setting is going to print well, even though you can still see some slight faceting. Our customer- centric approach ensures ICEM Surf continues to deliver a Class-A surfacing environment suitable for your real-world design requirements. It allows you to design models visually, and export them to JSON. If you can easily count the number of facets across your part, you need to increase resolution, and if you can't see any faceting at all, and your file size is very large (20+MB) you may need to decrease resolution. The latest release, ICEM Surf 2020, is generally available, the industry-leading Explicit Class-A surface modeling, analysis and visualization solution. MrCrayfishs Model Creator is a new and innovative 3D model editor for Minecraft. The following Custom Resolution settings are what was used for the red "Custom" sphere shown below.Ī good rule of thumb to determine whether or not your resolution is high enough is to try and count the triangles on your part. On the DXF Options page, select any options you wish. In the Export Options dialog, On the Scaling page, set the Scaling source to Map. These settings will suffice for most parts, but in some cases, it will be necessary to use a Custom Resolution to increase the number of triangles used. Silversurfer Galactus STL Files for 3D Printing and 3D Models - The models are optimized for all types of 3D Printing, SLA / SLS / FDM / DLP Types of 3D printing. Give the file a name, change the Save as type to DXF, check the box next to Selected objects only and click Save. For best results, output as Binary, and set Resolution to "Fine". This will unlock an "Options" button that will allow you to manually adjust the export settings.Ĭlicking the Options button will bring up the following window. In the Save As window, choose STL as file type. In SOLIDWORKS, simply go to File > Save As.
#SURFER 12 EXPORT 3D FILES HOW TO#
Today we will be talking about how to adjust the settings in SOLIDWORKS to achieve a good STL file for 3D printing. Just as it is possible to have too FEW triangles define your part, you can also overshoot and have too MANY triangles which creates a large file, and a level of detail that the printers can't achieve anyways. The level of triangulation, and effectively the amount of faceting, can be controlled during the CAD export to STL. Too few triangles, and a circle becomes a stop sign.
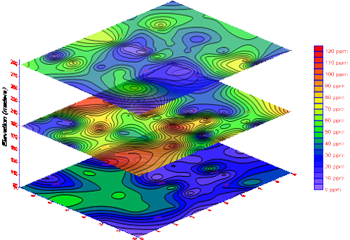
The amount of triangulation in the STL file will effect how faceted the surface of the part appears once printed. An STL file is a triangulated approximation of a 3D CAD model. Correctly converting CAD files into STL files is very important in order to print accurate parts.
